|
Connectivity: Smart Sensors or Smart Interfaces
James Wiczer, PhD
Sensor Synergy, Inc
Buffalo Grove, IL 60089
Abstract
Smart sensors devices may not be the universal panacea early proponents have suggested; other technologies, such as smart sensor interfaces, may provide essential tools to help make industrial processes more efficient and better integrate manufacturing operations with the rest of the enterprise.
Introduction
New smart sensing technologies rely on microelectronic processors to enable high-level processes at the sensor or actuator. These high-level processes often include network communications, sensor signal processing, and electronic datasheet features. Although there are many examples of smart sensor device technologies achieving technical goals, there are also too many examples of smart sensor development projects not achieving the target technical goals.
When considering the impressive technical accomplishments and cost reductions achieved by the microelectronics industry since the advent of the first microprocessor, one might be curious as to why all sensors are not smart sensors. Indeed, at the dawn of the 21st century, we have made significant progress in the 30+ years since the first, 2300-transistor, Intel 4004 microprocessor was introduced in 1971. Current technology provides us with complex new Pentium 4 microprocessors, which contain more than 42 million transistors and operate at speeds approaching 2 billion cycles per second. Where are the smart sensors? This paper will address this issue and answer the question - "Does it make sense to make all sensors smart sensors?"
Limitations to massive networks of smart sensors
Although it seems that the microelectronics industry might want to sell us large quantities of tiny silicon die loaded with the latest technology marvels to make our sensors smart, it may not be good for all sensor technologies. In fact, some have suggested that we should implement large networks of interconnected, smart sensors to better monitor and control our world.
However, massive networks of interconnected smart sensors have not yet been deployed in the real world and this is not likely to happen in the near term for two reasons: First, we do not yet have universally accepted standards to enable massive, inexpensive implementation of smart networked sensors. Second, there are major technology barriers that in some instances limit the implementation of highly integrated, smart networked sensors. Underlying both of these issues is the economic costs of acquiring and deploying smart sensors.
The first issue deals with non-technical issues associated with politics, intellectual property ownership, differentiating advantages in the marketplace and other "soft" issues. Several standards have been proposed and are currently under development including the IEEE 1451 series [1], the IEC 61158 (Foundation Fieldbus), Profibus, OPC, ModBus, CAN, DeviceNet, and many others [2]. These approaches provide "standards" for connecting sensors and actuators to networks and many of these are being implemented globally in industrial and commercial enterprises. Resolution of the "which standard" issue is beyond the scope of this paper.
The second issue relates to the physical limits of sensor technology implementations and must be assessed on a case-by-case basis when evaluating the wisdom of implementing a specific sensor in a smart form.
Physical limits to microelectronics intelligence and sensor element integration
Sensor technologies often exploit obscure physical effects to generate a sensed signal that can be used as a measurable indicator of a change of some physical state. The physical, chemical and electronic processes that underlie these sensing phenomenon can result in reliable and predictable sensor elements; however, these same processes make no claim regarding compatibility with microelectronic technologies. Often the materials, fabrication processes, or operations of these sensor technologies are inconsistent with the materials, fabrication processes, or operational requirements of microelectronics-based, "smart" capabilities. The process of tightly integrating intelligence into sensors requires the combination of mixed-mode integrated circuit fabrication technologies with the fabrication technology used to fabricate the sensor under consideration. These incompatibilities may require economically infeasible actions to circumvent.
The most straightforward example of this incompatibility is the case of a thermocouple required to operate at temperatures in the range of 300 C to 500 C. In addition to the fact that most microelectronic circuits do not survive at temperatures above 150 C, the materials used to make thermocouples are generally not compatible with the carefully controlled high purity materials used in silicon-based microelectronic fabrication processes. Trace amounts of common thermocouple metals such as chromium, nickel, iron, platinum, copper, and aluminum can appear to be dopant impurities to semiconductors. The presence of microscopic amounts of these metals during some of the microelectronic fabrication process steps can make the process fail.
Other sensors that may appear to be more likely candidates for tight integration of microelectronic-based "smart" features may also have limiting technical issues to consider. For example, changes in physical attributes like temperature, pressure, and acceleration are being sensed today by microelectromechanical systems (MEMS) technologies. MEMS sensors are generally silicon-based devices fabricated with microelectronics-compatible process technologies. However, the following examples will illustrate two situations in which silicon based sensing technologies are not amenable to the application of "smart sensor" technologies.
Economic limits to microelectronics intelligence and sensor element integration
Consider the implementation of a silicon-based, diaphragm-type, pressure transducer integrated with analog signal processing circuits and digital interfacing circuits. The essential elements found in "smart sensor" technology standards were designed into this device although this example was not specifically designed to meet the requirements of any single standard.
In analyzing this device, it is possible to correlate the signal processing circuits and analog interface circuits with many of the "smart sensor" functions specified in standards such as the IEEE 1451 . The digital interface circuits of this networked, smart sensor compares closely with many of the same functions described in the IEEE 1451 Network Capable Application Processor. The manufacturer of this development component learned that the integration of smart system interface elements and sensor elements onto a single silicon chip created unanticipated problems [3]. For example, the cost of the package that provided both exposure to environmental gas pressure changes and also provided the necessary number of microcontroller driven electrical interconnections was prohibitively high for the intended application.
In this application, a key requirement for pressure sensors is the exposure of the sensing element to the outside environment where the pressure changes occur. This exposure had the potential for a negative impact on the reliability of the complex, companion microcontroller digital circuits. In general, complex digital electronic circuits operate better when isolated from contaminants in the environment. Beyond packaging costs and reliability issues, the cost of development to merge two, somewhat incompatible, technologies can also make the resulting devices prohibitively expensively.
Another example of a problematic highly integrated "smart sensor" was a smart hydrogen sensor developed at Sandia National Laboratories. [4]. A network interfaced, silicon-based smart hydrogen sensor, as shown in Figure 1, was designed and fabricated with integrated sensor elements, sensor bias, sensor signal processing, analog-to-digital conversion for the sensor signal and a digital network interface. Sandia scientists and development engineers needed to solve difficult materials compatibility issues associated with integrating hydrogen sensor technology with silicon analog and digital circuits technology. The hydrogen sensor used metals that were fundamentally incompatible with microelectronic fabrication technologies. The technical problems for this smart sensor were eventually surmounted but significant process modifications needed to be developed. The additional processing and engineering costs of the solution may make this smart networked hydrogen sensor prohibitively expensive to manufacture.
|
 |
 |
Figure 1. Smart hydrogen sensor with network capabilities. |
Figure 2. Basic hydrogen sensor element |
After the technology was successfully demonstrated, Sandia National Laboratories licensed the basic hydrogen sensor technology to industrial concerns for commercial manufacture. In the commercial form of this device, the hydrogen sensor element, resistance heaters, and temperature sensors were fabricated on one chip and the signal processing, temperature control signals and network functions were performed off-chip by various standard components. The most basic form of this sensor, prior to commercialization, is shown in Figure 2. In addition to the different magnifications of the photographs reproduced in Figures 1 and 2, note the stark contrast in microelectronic complexity between the two devices.
The separation of the sensing element from the network and signal processing electronics had some advantages by providing greater flexibility for hydrogen sensor applications in certain extreme environments. In this example, the separation between smart circuits and the basic sensor element is made possible by applying temperature control techniques to the hydrogen-sensing element. In operation, the sensor can be considered as a simple resistive circuit element, which further simplifies the remote electronic interface to the sensing element.
The feature enhancements of smaller size and lower weight associated with highly integrated smart sensors may not be of interest to users due to the added costs and manufacturing difficulties for the networked smart hydrogen sensor. It is possible that future users may require smaller size and lighter weight for microrobotics, space applications, or other low-volume and low-weight applications.
User implementation costs
In evaluating the potential for integrating sensor technologies with network and signal processing intelligence, end-user implementation costs must also be considered. Many sensors are used in constrained applications that would not benefit from the features of smart sensors. Depending on the details of the application, the added cost of smart-sensor software interfaces, software compatibility issues, and other software field maintenance issues may make it infeasible to consider smart sensor technologies. From the perspective of the sensor application engineers, the added cost, interface complexity, and associated decreased reliability for a smart sensor over the plain unenhanced version of the same sensor, may make the unenhanced sensor the optimum choice for some applications.
In evaluating the potential for integrating sensor technologies with network and signal processing intelligence, end-user implementation costs must also be considered. Many sensors are used in constrained applications that would not benefit from the features of smart sensors. Depending on the details of the application, the added cost of smart-sensor software interfaces, software compatibility issues, and other software field maintenance issues may make it infeasible to consider smart sensor technologies. From the perspective of the sensor application engineers, the added cost, interface complexity, and associated decreased reliability for a smart sensor over the plain unenhanced version of the same sensor, may make the unenhanced sensor the optimum choice for some applications.
Guidelines for smart sensor implementation
Materials and process technologies used in the fabrication of sensor elements need to be evaluated with respect to the process requirements for mixed mode (analog and digital) microelectronics technologies. In addition, typical operational modes for the sensor under consideration must be compatible with microelectronics circuit limitations. Although these two criteria seem straightforward, hidden or unstated operational requirements and proprietary sensor element materials may erroneously make a sensing technology appear to be amenable to smart sensor fabrication processes.
Alternate fabrication techniques, such as hybrid microelectronic fabrication processes, may reduce or eliminate some of the fabrication incompatibility problems for some smart sensors. Hybrid microelectronic fabrication technologies allow for elements fabricated with incompatible processing technologies to be mechanically and electrically joined on a common substrate. Although hybrid processes can reduce some of the processing incompatibilities, operational issues must be carefully analyzed prior to launching a hybrid smart sensor fabrication effort. In addition, hybrid manufacturing processes tend to be significantly more expensive than monolithic integrated circuit manufacturing processes.
For example, although a micromachined, diaphragm-type pressure sensor may appear ideally suited for tight integration with signal processing and digital network interface circuitry, operational requirements may reduce overall device reliability to unacceptable levels. In contrast, vibration and acceleration sensors using similar technology but not exposed to the external environment, may be very well suited for "smart sensor" integration efforts.
Although it may seem like heresy to argue against the "smart" concept, for some applications "not-smart" or "dumb" sensors are smart to use. It just may not be smart to tightly integrate "smart" enabling electronics with all sensor components. In some cases, "smart" interfaces may provide the desired networking features without imposing the technical compatibility and cost requirements on the sensor fabrication technology.
Moving the line
The best approach for implementing some smart sensor technologies may not be to monolithically integrate sensing elements with microelectronics intelligence onto a single silicon die. If we consider the package containing our functional blocks as a "line", we should consider moving the line - or moving the package envelope - to include fewer of the functional blocks required to make a sensor a smart sensor. Should sensor elements, signal-processing circuits, interface circuits, sensor specific electronic datasheets and network circuits be in the same package or should we move the line?
As noted above for the case of the hydrogen sensor, the commercial form of this device was designed and fabricated to include on the sensor chip with the hydrogen sensing element only the technically necessary ancillary elements such as the heater elements and the temperature sensor elements. The other elements, including the high level signal processing and digital network interfaces, were situated in close proximity to the sensing chip but not integrated on the same chip as the hydrogen sensor. Situating these other elements "off-chip" reduced costs and enhanced design flexibility by enabling the use of a variety of "off-the-shelf" circuits to complete the necessary function blocks for a smart sensor subsystem.
Given the technological and economic limitations associated with tightly integrating smart microelectronics circuits with certain types of sensing elements, perhaps we should broaden our definitions and consider alternate solutions. Instead of smart sensor devices, maybe we need to consider smart sensor solutions or smart sensor subsystems?
It seems that some highly integrated, smart sensor technologies will be successful devices such as vibration sensors and moderate-environment, temperature sensors. But for others we may need to make adaptable smart interfaces that combines the functionality of signal processing circuits, interface circuits, sensor specific electronic datasheets, and network circuits into a single smart sensor interface that serves as the intermediary to connect networks to sensors.
There are now available adaptable smart transducer interface units that provide many of the more useful features of standards such as the IEEE 1451.2 and include an adaptable feature that make these interface units able to connect to a broad array of sensor types. This approach provides for some of the key features of smart sensor technologies such as sensor-specific, electronic data sheets and self identification capabilities without requiring sensor manufacturers to re-work their product offerings by tightly integrating microelectronic-based intelligence into their sensors.
There seems to be a paradox in which smart sensors may be desirable from the perspective of remote-access, sensor-specific electronic datasheets, and network interface features yet the economic and technical barriers may make smart sensors undesirable. The solution to this paradox may be the use of "smart and adaptable" sensor interfaces. There are many applications in which the features of smart-sensor technologies would be highly beneficial. However, instead of trying to get sensor component manufacturers to provide "smart" versions of each sensor in their catalog, perhaps we should consider the use of smart and adaptable sensor interface units. These smart interfaces would enable the use of one's favorite, existing sensor component in applications that require "smart", networked sensors.
Smart interfaces for unenhanced sensors
An example of applying this adaptable smart interface technology, is described here for a special chemical sensor. The sensor was developed by scientists and engineers at Sandia National Laboratories in response to a need to monitor trace contaminants of volatile organic compounds. These contaminants were suspected of being in the ground near various U.S. Department of Energy legacy waste sites. The selected sensor technology used specially coated quartz crystal microbalance sensors in which the frequency of oscillation of a crystalline quartz resonator [5]. Researchers deposit specially designed chemically absorbing polymer layers on the surface of crystalline quartz resonator disks to fabricate the sensor. This thin, polymer film will selectively absorb chemical contaminants from the resonator's environment while situated on top of the resonating quartz disk. As the film absorbs more or less of the target chemical, the mass and stiffness of the film change through mechanical loading effects. A sensing effect is created as the resonator's frequency of oscillation and damping factors change with contaminant induced film changes [6]. An exceptionally sensitive, chemical contaminant sensor results from careful calibration and numerical transformations of the temperature dependent frequency shifts and damping voltage changes.
Due to the mechanical isolation requirements for the 2.5 cm resonator disk, the severe environments for the intended application, the discrete nature of the radio frequency drive circuits [7], and small number of specialized sensors ultimately required for this market segment, a tightly integrated smart sensor solution was not considered feasible. However, an adaptable smart interface, such as the one developed by Sensor Synergy, seemed well suited for this application.
The smart, adaptable sensor interface approach used for this project, provided the desired network connectivity, form factor features, cost goals, and met the physical constraints of the sensor's environment. The sensor test application required the ability to make remote sensor data readings via http protocol with physically remote client computers utilizing "browser" programs as shown in Figure 3. In addition, three sensor readings within a one second trigger window were required for this smart sensing application to derive valid contamination sensor data. Separate measurements for frequency change, temperature, and damping voltage were all made within the required one second trigger window and reported to each connected browsers.
The completed solution included the ability to customize the displayed "web" page and to modify certain fields in the sensor's electronic data sheet. The interface also included an actuator signal for future use of controlled contaminant sources for remote re-calibration. A version of this system has run continuously for nine months without difficulty.
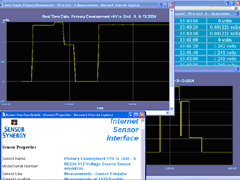
Figure 3. Sample Web page generated by Adaptable Smart Transducer Interface
Conclusions
We have described some real-world examples of smart sensor device technologies with significant technical and economic feasibility concerns. We have also described an example of a smart sensor interface applied to an unenhanced sensor to create a functioning smart sensor unit. The smart interface example described here provided the key features of the IEEE 1451.2 smart sensor standard including a sensor specific electronic datasheet and network interface functions in this case compatible with Ethernet-based, hypertext transaction protocol. The use of the smart sensor interface avoided the economic and technical challenges of a more tightly integrated smart sensor device approach.
Acknowledgements
The author wishes to acknowledge the scientists and engineers at Sandia National Laboratories in Albuquerque, New Mexico for their helpful suggestions and sensor data. Special thanks are due to Dr. Robert C. Hughes, Dr. Richard W. Cernosek and Dr. Stephen J. Martin for their insightful comments and useful critiques.
References
[1] IEEE Std 1451.2-1997, "IEEE Standard for a Smart Transducer Interface for Sensors and Actuators - Transducer to Microprocessor Communication Protocols and Transducer Electronic Data Sheet (TEDS) Formats", IEEE Instrumentation and Measurement Society, TC-9 Committee on Sensor Technology, Institute of Electrical and Electronics Engineers - IEEE, New York, N.Y., Sept. 1998.
[2] Crovella, Robert M., "Sensor Networks and Communications", The Measurement, Instrumentation, and Sensors Handbook, ed. Webster, John G., CRC Press/ IEEE Press, Boca Raton, FL, 1999, pages 88-1 to 88-18.
[3] Frank, Randy and Zehrbach, D.; "Testing the System on a Chip" Sensors, vol. 15, No. 9., Sept. 1998.
[4] Rodriguez, J. L., Hughes, R.C., McWhorter, P. J., "Robust, Wide range Hydrogen Sensor" IEDM Extended Abstracts 1992 . IEDM Technical Digest, IEEE cat. # 92CH3211-0 pg. 521-524 (1992).
[5] Martin, S. J. and Frye, G. C., "Polymer Film Characterization Using Quartz Resonators," Proc. 1991 IEEE Ultrasonics Symposium, pp. 393-398 (IEEE, New York, 1991).
[6] Martin, S. J., Cernosek, R. W., and Spates, J. J., "Sensing Liquid Properties with Shear-Mode Resonator Sensors," Proc. Transducers 95/Eurosensors IX, Stockholm, Sweden (1995).
[7] Cernosek, R.W., Martin, S. J., Wessendorf, K. O., Terry, M. D., and Rumpf, A. N., "Quartz Resonator Fluid Monitors for Vehicle Applications," Proc. Sensors Expo, pp. 527-539 (1994).
|
|
|
|
|